
液位產(chǎn)品導(dǎo)航
磁翻板液位計
磁敏電子雙色液位計 專用遠傳變送器 專用報警開關(guān) 電加熱磁翻板液位計 真空夾套型磁翻板液位計 蒸汽夾套磁翻板液位計 鈦合金磁翻板液位計 帶遠傳磁翻板液位計 頂裝磁翻板液位計 pp材質(zhì)防腐磁翻板液位計
玻璃管液位計
螺紋玻璃管液位計 玻璃管液位計 不銹鋼管式帶扣304玻璃 小型管式液位計 玻璃管液位計超聲波液位計
分體式超聲波物位計(標 分體式超聲波液位計(精 分體式超聲波物位計 一體式超聲波液位計(雷達液位計
石英管液位計
石英管式雙色水位表 X49H平板鍋爐水位計 B49H型鍋爐雙色水位表 彩色石英管液位計浮球液位計
液位變送器
靜壓高溫投入式液位變送 靜壓投入式液位變送器 直桿式液位變送器 平衡罩式液位變送器 電感式液位變送器 防腐投入式液位變送器 雙法蘭液位變送器 LY-600系列電容液位計射頻導(dǎo)納物位計
浮球液位開關(guān)控制器
浮式磁翻板液位計生產(chǎn)流程控制系統(tǒng)設(shè)計與實現(xiàn)
作時間:2019-10-29 16:45:20 來源: 作者:
摘要:浮式磁翻板液位計長期海上工作,受場地和環(huán)境限制,油氣處理磁翻板液位計集成度高,控制難度大等特點。為驗證FPSO生產(chǎn)流程控制系統(tǒng)(productioncontrolsystem,PCS)的總體設(shè)計和關(guān)鍵技術(shù),以某30萬噸FPSO為研究對象,針對油氣處理工藝特點,介紹了PCS系統(tǒng)組成、三相分離器的控制策略及PCS樣機的功能測試方法,為今后其他FPSO生產(chǎn)流程PCS系統(tǒng)的總體設(shè)計和解決方案提供參考。
0引言
海上浮式生產(chǎn)儲油卸油裝置集生產(chǎn)處理、儲存外輸及生活、動力供應(yīng)于一體,把來自油井的油氣水等混合液進行粗加工處理,處理后的成品原油儲存于貨油艙,到一定儲量時經(jīng)過外輸系統(tǒng)輸送到穿梭油輪。作為海上石油生產(chǎn)的核心,受環(huán)境限制較多,油氣加工處理磁翻板液位計集成度高,生產(chǎn)工藝復(fù)雜,生產(chǎn)過程中一旦發(fā)生意外,將對環(huán)境造成傷害和不可挽回的損失[1],因此對整個生產(chǎn)流程系統(tǒng)提出了很高控制要求。為此,基于對FPSO控制系統(tǒng)功能需求分析,研究其關(guān)鍵控制技術(shù),構(gòu)建了參數(shù)自整定模糊PID控制系統(tǒng),并給出了樣機的功能測試方法,為其他FPSO生產(chǎn)流程控制系統(tǒng)(productioncontrolsystem,PCS)的總體設(shè)計和關(guān)鍵技術(shù)解決提供了良好參考。
1系統(tǒng)功能需求
FPSO控制系統(tǒng)主要功能模塊包括:油氣水處理(PCS)模塊、儲卸油模塊、發(fā)電模塊、生活模塊和系泊模塊等。其中,核心PCS模塊包括:原液輸送系統(tǒng)、油氣分離系統(tǒng)(多次分離)、生產(chǎn)水處理系統(tǒng)、天然氣處理系統(tǒng)、火炬放空系統(tǒng)、計量系統(tǒng)、化學藥劑系統(tǒng)和開閉排系統(tǒng)等。以恩平油田FPSO為例,原油處理包括三級處理流程、生產(chǎn)水采用兩級處理流程。該FPSO處理能力:油9000m3/d、液13000m3/d、氣60930m3/d及生產(chǎn)污水7200m3/d;輸出原油要求含水率0.5%以下[2]。PCS工藝流程如圖1所示。由圖1可知,油氣原液經(jīng)過斷塞流捕集器后加熱進入油水氣分離磁翻板液位計,通過加入藥劑使原油乳狀液變得更加穩(wěn)定,流入沉降分離室作進一步沉降分離,以降低原油的含水量[3],分離出的原油再經(jīng)過電脫水器處理后達到可存儲外輸標準。原油處理工藝段為PCS主要工藝段,分離器為核心工藝磁翻板液位計。由于FPSO場地有限,不能建類似陸地上大的沉降池,因此對分離設(shè)備(三相分離器)提出較高的控制要求,如果兩次分離沒有達到預(yù)計效果,將進行第三次分離,分離次數(shù)多會增加原油的采收成本。
2系統(tǒng)設(shè)計
2.1系統(tǒng)架構(gòu)
為實現(xiàn)油氣處理功能,PCS控制系統(tǒng)總體設(shè)計采用智能儀表、計算機自動控制和分布式接口等先進技術(shù),通過網(wǎng)絡(luò)集成平臺,構(gòu)建自動化集成系統(tǒng)綜合監(jiān)控,實現(xiàn)管理控制系統(tǒng)控制一體化。
根據(jù)FPSO生產(chǎn)工藝系統(tǒng)流程劃分,同時考慮工藝磁翻板液位計位置分布,PCS過程控制系統(tǒng)硬件架構(gòu)以羅克韋爾自動化硬件為主,其中CPU電源、CPU模塊和通信等部分采用冗余配置。設(shè)計方案采用主處理器單元(CC)、遠程機架(ET1~5)、網(wǎng)絡(luò)磁翻板液位計等組成,
PCS控制系統(tǒng)網(wǎng)絡(luò)配置如圖2所示。主處理器單元和遠程機架可根據(jù)工藝磁翻板液位計布局、信號采集點分布情況,集中或分散安裝到控制柜中進行現(xiàn)場信號收集。系統(tǒng)由三層網(wǎng)絡(luò)組成,包括設(shè)備網(wǎng)(ControlNet)、控制網(wǎng)(TCP/IP)、管理網(wǎng)(TCP/IP)以及無線網(wǎng)。控制網(wǎng)與管理網(wǎng)采用雙光纖環(huán)網(wǎng)冗余配置,配備帶有雙光口多電口的高速網(wǎng)絡(luò)交換機。在管理網(wǎng)層,主要由冗余數(shù)據(jù)服務(wù)器、工程師站和操作員站構(gòu)成分布式結(jié)構(gòu),采用基于服務(wù)器/客戶端的結(jié)構(gòu)靈活、功能強大的組態(tài)軟件,完成整個PCS過程控制系統(tǒng)的動態(tài)信息顯示、工藝參數(shù)顯示與設(shè)置、工藝磁翻板液位計的控制與操作、數(shù)據(jù)管理、報警、安全控制及報表統(tǒng)計與打印,并且包含與ESD系統(tǒng)、FGS系統(tǒng)等其他系統(tǒng)數(shù)據(jù)通信功能。
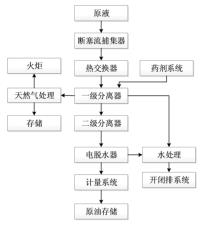
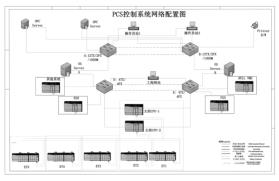
2.2控制功能
PCS系統(tǒng)是實現(xiàn)FPSO各工藝段的生產(chǎn)流程控制、報警、測量、數(shù)據(jù)獲取、監(jiān)視以及控制FPSO和井口平臺流程的功能,系統(tǒng)特別強調(diào)生產(chǎn)在線及安全功能,需要研究系統(tǒng)在故障情況下能持續(xù)運行的控制策略。PCS的軟件設(shè)計包括故障模式分析、冗余設(shè)計和容錯設(shè)計,根據(jù)傳感器的冗余形式建立一套基于可尋址及帶表決功能的軟件系統(tǒng),在軟件結(jié)構(gòu)上同時建立正常流程和故障處理流程,較大限度保證故障安全性,較終形成具有一定安全等級的軟件體系。具體功能包括以下幾項:
(1)提供動態(tài)的生產(chǎn)流程信息監(jiān)控。
(2)主要工藝參數(shù),監(jiān)視生產(chǎn)模塊磁翻板液位計的運行情況顯示。
(3)處理報警事件。
(4)滿足生產(chǎn)系統(tǒng)邏輯連鎖及控制要求。
(5)與其他系統(tǒng)實現(xiàn)數(shù)據(jù)交換。
3關(guān)鍵磁翻板液位計控制技術(shù)
FPSO原油處理工藝段中有多個控制設(shè)備,包括:斷塞流捕集器、三相分離器和電脫水器等。三相分離器為核心磁翻板液位計,三相分離器的工作原理是以油井來液的相應(yīng)密度差為動力,使進入容器內(nèi)的油氣水經(jīng)揮發(fā)、分離和沉降等過程后,分別進入到氣相室、油室和水室,再經(jīng)各自出口管匯計量后控制外排。圖3為臥式三相分離器原理圖,進料是油氣水三相混合流(油氣比例變化較大),通過斷塞流捕集器調(diào)節(jié)后,管道進液趨于穩(wěn)定,通過加入破乳劑作為脫水劑,加速將原油中的水分脫出來,以保證生產(chǎn)連續(xù)性。
本文以三相分離器中破乳劑添加量控制為例,介紹提升破乳劑實用效率以達到降低原油采收成本的控制策略。傳統(tǒng)控制模式(見圖4)根據(jù)進油管道總流量為輸入量,設(shè)定濃度為偏差,采用PID控制[4],實現(xiàn)破乳劑加入量的閉環(huán)控制[5-7]。
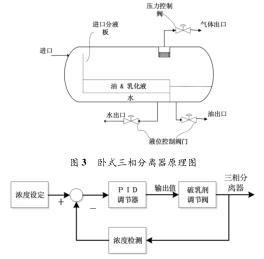
液體滯留時間是一個間接用于確定處理一定液體流量所必需的分離器體積的方法。分離器的液體體積等于液體流量乘以滯留時間,常用下式計算滯留時間。

式中:V為所需的分離器液體部分的容積,m3;Q為液體流量,m3/d;T為滯留時間,min。三相分離器內(nèi)的氣體壓強,可以根據(jù)理想氣體狀態(tài)方程得到:

式中:P為指理想氣體的壓強,Pa;V為理想氣體的體積,m3;n為氣體物質(zhì)的量,kg/mol;T為理想氣體的熱力學溫度,℃;R為理想氣體常數(shù)。
根據(jù)式(1)、式(2)建立三相分離器動態(tài)數(shù)學模型。假設(shè):①物料在三相分離器內(nèi)時間可以忽略;②進液總管流量Q總不變;③分離器內(nèi)溫度恒定[8],得到以下動態(tài)數(shù)學模型:
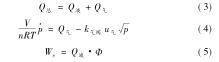
式中:Q總為總管流量,kg/s;Q液為進液體流量(油和水混合物),kg/s;Q氣為進氣流量,kg/s;p為氣體壓力,Pa;V為分離器內(nèi)氣體體積,m3;n為氣體摩爾質(zhì)量,kg/mol;R為氣體定律的常數(shù),J/(kmol·K);k氣閥為排氣閥的流量系數(shù);u氣為氣體流速,m/s;We為破乳劑加入量,kg/s;Ф為破乳劑加入因數(shù)。分析系統(tǒng)模型式(3)~式(5)可知,假設(shè)分離器進液總量不變,內(nèi)氣體體積恒定、出油口閥門開度不變,氣體壓力只與進液的成分有關(guān),即:進液中原油和水的混合比例發(fā)生變化或原油中氣體含量發(fā)生變化。
如果采用圖4總管流量PID調(diào)節(jié)破乳劑加入量控制,則出水口的含油率可產(chǎn)生較大變化,這是因為忽略了進液成分變化導(dǎo)致氣體壓力變化,從而不能準確判斷破乳劑的加入量,所以在本控制系統(tǒng)中加入?yún)?shù)自整定模糊控制器[9],如圖5所示。在常規(guī)PID基礎(chǔ)上,把出水口含油量偏差We作為觀察量、破乳劑加入量Wec作為控制量,進行模糊化處理。建立We模糊合集:負大(NB)、負小(NS)、零(ZO)、正小(PS)、正大(PB);建立控制量Wec模糊合集:負大(NB)、負小(NS)、零(ZO)、正小(PS)、正大(PB)。采用We增加則Wec增加、We減小則Wec減小的模糊規(guī)則,形成模糊關(guān)系矩陣:Wec=We·R。使用加權(quán)平均法反模糊化輸出模糊決策,通過調(diào)整PID調(diào)節(jié)器的Kp、Ki、Kd,實現(xiàn)控制輸出的快速響應(yīng)。通過參數(shù)自整定模糊PID控制,根據(jù)被控對象的變化,實現(xiàn)控制的快速反應(yīng),提高控制精度。
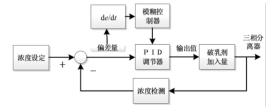
4系統(tǒng)實現(xiàn)
化工流程模擬技術(shù)是以工藝過程的機理模型為基礎(chǔ),采用數(shù)學方式來描述化工過程,通過應(yīng)用計算機輔助計算手段,進行過程物料衡算、熱量衡算、設(shè)備尺寸估算和能量分析,作出環(huán)境和經(jīng)濟評價,實現(xiàn)優(yōu)化生產(chǎn)、節(jié)約資源和提高經(jīng)濟效益的目的[10]。為了驗證系統(tǒng)的有效性和功能性,參照石油化工行業(yè)加工制造標準及中國船級社相關(guān)制造標準,研制了PCS系統(tǒng)功能樣機[11-16]。根據(jù)FPSO的PCS過程控制系統(tǒng)設(shè)計方案及各工藝流程劃分,考慮原油處理工藝段控制設(shè)備多、工藝復(fù)雜和控制難度大等因素,選用主處理器單元(CC)、遠程機架ET1、ET2為試驗樣機。樣機具備30萬噸FPSO的原油處理系統(tǒng)中的所有工藝生產(chǎn)流程控制、邏輯聯(lián)鎖、監(jiān)控報警及與其他系統(tǒng)的數(shù)據(jù)通信等功能。
4.1系統(tǒng)軟件功能實現(xiàn)
PCS系統(tǒng)軟件設(shè)計基于Rslogix5K和FactoryTalkView平臺,參照油氣處理工藝流程設(shè)計PLC程序系統(tǒng)。參照油氣處理工藝流程設(shè)計PLC程序系統(tǒng)結(jié)構(gòu)見圖6。
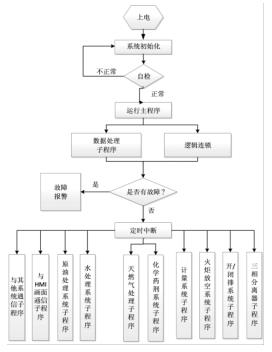
4.2系統(tǒng)樣機功能測試
通過專用設(shè)備“模擬屏”和“計算機數(shù)據(jù)仿真”模擬原油處理工藝,進行功能性試驗,如圖6所示。根據(jù)原油處理工藝流程設(shè)計了型號為VR_SIM的模擬屏,模擬屏上可以顯示一級、二級分離器等設(shè)備狀態(tài),模擬屏有指示燈、電位計和按鈕等。通過電位計模擬溫度、液位及壓力的變化,按鈕模擬開關(guān)量設(shè)備的變化,觀察模擬屏各個設(shè)備的狀態(tài)顯示(也可以通過HMI觀察),來驗證原油處理工藝段程序控制的正確性。為全面測試PCS控制系統(tǒng)控制功能,系統(tǒng)中還設(shè)計了計算機數(shù)據(jù)仿真模塊。通過計算機數(shù)據(jù)仿真模塊模擬現(xiàn)場信號,可加載的信號包括:生產(chǎn)水處理系統(tǒng)、天然氣系統(tǒng)、火炬防空系統(tǒng)、化學藥劑系統(tǒng)、開/閉排系統(tǒng)、原油外輸系統(tǒng)和惰性氣體系統(tǒng)等工藝流程中的設(shè)備,管路上的開關(guān)量信號、模擬量信號,以及現(xiàn)場總線方式通信信號等。主處理器單元收到計算提供的信號后,可識別出磁翻板液位計的運行狀態(tài),根據(jù)預(yù)設(shè)的控制策略進行設(shè)備控制,由HMI監(jiān)控畫面展示設(shè)備運行狀態(tài),達到驗證PCS控制系統(tǒng)的全部控制功能。通過模擬屏和計算機數(shù)據(jù)仿真,可以實現(xiàn)FPSO流程生產(chǎn)運行情況的動態(tài)管理和分析。針對典型生產(chǎn)情況,為事故預(yù)測和診斷專家系統(tǒng)提供模擬環(huán)境,同時對現(xiàn)場人員進行培訓,熟悉工藝流程和現(xiàn)場操作,了解工藝機理,能夠縮短現(xiàn)有技術(shù)中操作工人和技術(shù)人員面對油氣生產(chǎn)處理過程中處理故障的時間和極端情況下不能及時作出反應(yīng)等問題,保證了生產(chǎn)安全和生產(chǎn)效率。
5結(jié)束語
本文FPSO生產(chǎn)流程PCS控制系統(tǒng)研制技術(shù)路線包括:依據(jù)某30萬噸FPSO功能需求開展頂層設(shè)計,堅持自主研發(fā)和消化吸收國外先進技術(shù)相結(jié)合的原則,滿足國際規(guī)范相關(guān)標準,按照“原油處理系統(tǒng)、水處理系統(tǒng)、加藥系統(tǒng)、天然氣系統(tǒng)、原油外輸系統(tǒng)”工藝劃分,采用精密測量、網(wǎng)絡(luò)通信、計算機控制、PLC控制和傳感器技術(shù),通過網(wǎng)絡(luò)集成平臺,構(gòu)建自動化集成系統(tǒng)綜合監(jiān)控,實現(xiàn)對石油生產(chǎn)流程中的關(guān)鍵技術(shù)攻關(guān)和掌握。采用仿真和試驗相結(jié)合的研究方法,完成了PCS系統(tǒng)的核心控制策略和工程樣機試驗技術(shù)的研究工作。通過PCS樣機功能測試,驗證系統(tǒng)設(shè)計的正確性和合理性,及時發(fā)現(xiàn)問題并處理,避免危險工況下的測試風險,裝配出滿足海工平臺使用要求的工程樣機。
最新資訊
- [公司新聞] 磁翻板液位計有測量盲區(qū)嗎 2021-12-06
- [行業(yè)新聞] 差壓變送器該怎么維護 2021-11-29
- [行業(yè)新聞] 浮球液位計保養(yǎng)時注意事項 2021-11-25
- [公司新聞] 磁敏雙色液位計與磁翻板液位計有什么區(qū)別 2021-11-16
- [公司新聞] 造成磁翻板液位計內(nèi)浮子下沉的常見原因都 2021-11-10
推薦專題
- [行業(yè)新聞] 玻璃管液位計的應(yīng)用 2020-08-01
- [技術(shù)專題] 石油儲罐液位測量選擇雷達液位計后的安裝 2012-10-26
- [技術(shù)專題] 超聲波液位計的優(yōu)點和清洗方式 2012-10-20
- [技術(shù)專題] 怎樣選購高溫高壓型磁翻板液位計 2012-10-20